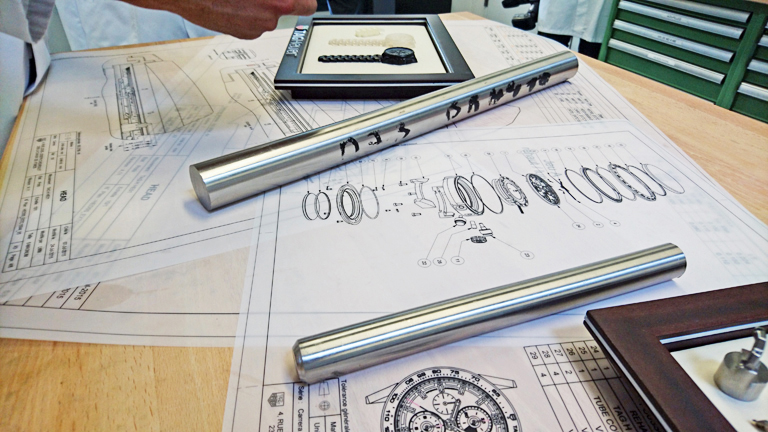
Watch manufacturers are notoriously secretive when it comes to the design and production of their timepieces, which makes it all the more surprising when you're invited to take a tour of the TAG Heuer factory. The watchmaking process has remained relatively unchanged over the years, but the Swiss company is keen to move with the times, which has resulted in it releasing the TAG Heuer Connected, an Android-based smartwatch. However, the company hopes that this move will ultimately attract younger tech fans towards the more conventional timepieces in its range.
A long history
Much of the day for technicians is spent peering through a magnifying glass
Edouard Heuer founded the company in nearby Saint-Imier way back in 1860, but today the central hub of the TAG Heuer operation is housed in a very modern building in La Chaux-de-Fonds, not far from Neuchâtel. You get a real sense of the heritage as you walk through the front doors of this plush factory, particularly within the confines of the in-house museum. Our 'tour guide' looks after the collection, which is housed in a darkened room bristling with models from down the years, including the original and highly distinctive 1969 Steve McQueen Monaco model that was popularised by the Hollywood actor in the 1971 movie Le Mans.
The headquarters
Every watch case is crafted from a piece of solid bar
There are other satellite manufacturing buildings dotted around the Swiss countryside, with one dedicated solely to producing dials for the range and another for creating the all-important movements, but it's this place where all those component parts come together to make a TAG Heuer. And, there are many parts, which means that modern manufacturing methods have transformed the way the business operates. TAG Heuer produces large volumes of wristwatches including the Formula One, Aquaracer, Link and Carrera to name but a few, and while the emphasis is still on quality, there is a definite whiff of production line mentality about the place.
The design
Fingertips need to be kept away from surfaces to avoid the transfer of grease and dirt
Our guide, resplendent in a black lab coat, concedes that the bulk of their clients are male and this has shaped the design aspect of new models. Even the watches created for women have a slightly macho feel to them. Nevertheless, every model starts out at the same point in a small room at the top of the building. Product developers, engineers and designers work together on the movement, the case, dials, hands and the bracelet using a blend of computer-aided design and old-school technical drawings to build up a profile of each new model.
Get all the latest news, reviews, deals and buying guides on gorgeous tech, home and active products from the T3 experts
The laboratory
The company has recently developed a bespoke solution for check if watches are watertight
Once all of the research and development has been done, and prototype components produced, it's onto the test laboratory. This place has been nicknamed the 'Torture chamber' and for good reason. Inside a collection of stuffy rooms there are a raft of quirky machines, many of which look handmade for the unusual tasks they have to do. There are gizmos that shake and vibrate, others that push and pull, which allows the TAG Heuer team to test every facet of a new watch. The aim is to recreate the lifecycle of a product in a short space of time.
There are machines that test how your watch will fare when dropped from a specific height
So watch bracelets, for example, take a pounding inside industrial polishers that have been repurposed to emulate years of wear and tear. There's a machine to check moisture levels and another for analysing waterproofing seals; heck, there's even a hammer on a pendulum that's used to test shockproof capabilities.
Step-by-step
An array of new dials and movements wait for their cases
With a new design approved and tested, production itself involves a whole variety of stages with, initially, the manufacture of components. Once these pieces have been created the pre-assembly of various mechanisms begins. After that, all of the sub-assemblies are brought together to complete the watch movement. High-tech Fluery modulo production systems at the movement factory over at nearby Chevenz allows the company to produce a wide variety of model variants, while at the same time retain the pinpoint precision needed to create chronograph movements.
Manufacturing magic
Component parts are created using an array of CNC machines
Largest component of the lot is the body, which is honed from solid blocks of metal; aluminium for the most part, using CNC machines watched over by keen-eyed technicians. TAG Heuer has also moved with the times and pushed forwards with a raft of innovative design and manufacturing techniques. Most notable of these developments has been the move towards belt driven movements as opposed to the more traditional gears found in traditional wristwatches. And, when it comes to belts then these are some of the smallest you're ever likely to encounter, with some being the same thickness as a human hair.
Final assembly
Dials and hands are carefully atatched to the watch face
The staff here start early; 6am for many, and they take a lot of breaks but that's hardly surprising when you see the sort of work they do. Sitting at neat rows of desks the technicians carefully put together the components following around 100 processing steps in all. TAG Heuer gives all of the production stages a 'T' abbreviation, so T2 and T3 are the departments that carry out final assembly. Straps or bracelets are added, labels and paperwork included and the final timepiece is ready to go for final testing.
Quality control
The work is painstaking and requires employees to take frequent breaks
Despite the meticulous attention to detail when producing a TAG Hueur wristwatch it's inevitable that one or two models will have a fault, either with the fit or the finish. Staff carry out batch checks on newly created watches and, if anything isn't quite right, then it's back to the production team for additional tweaks. Our guide explains that the eighties wasn't a great period for the business, which resulted in the TAG Group acquiring a major share in Heuer and changing the company forever. However, right now, things look very rosy thanks to the Connected smartwatch and the ever growing range of traditional timepieces.
A finished TAG Hueur Connected that, as you can read about in T3's official review, we really liked
Rob Clymo has been a tech journalist for more years than he can actually remember, having started out in the wacky world of print magazines before discovering the power of the internet. Since he's been all-digital, he has run the Innovation channel for a few years at Microsoft, as well as turning out regular news, reviews, features and other content for the likes of Stuff, TechRadar, TechRadar Pro, Tom's Guide, Fit&Well, Gizmodo, Shortlist, Automotive Interiors World, Automotive Testing Technology International, Future of Transportation and Electric & Hybrid Vehicle Technology International. In the rare moments he's not working, he's usually out and about on one of the numerous e-bikes in his collection.