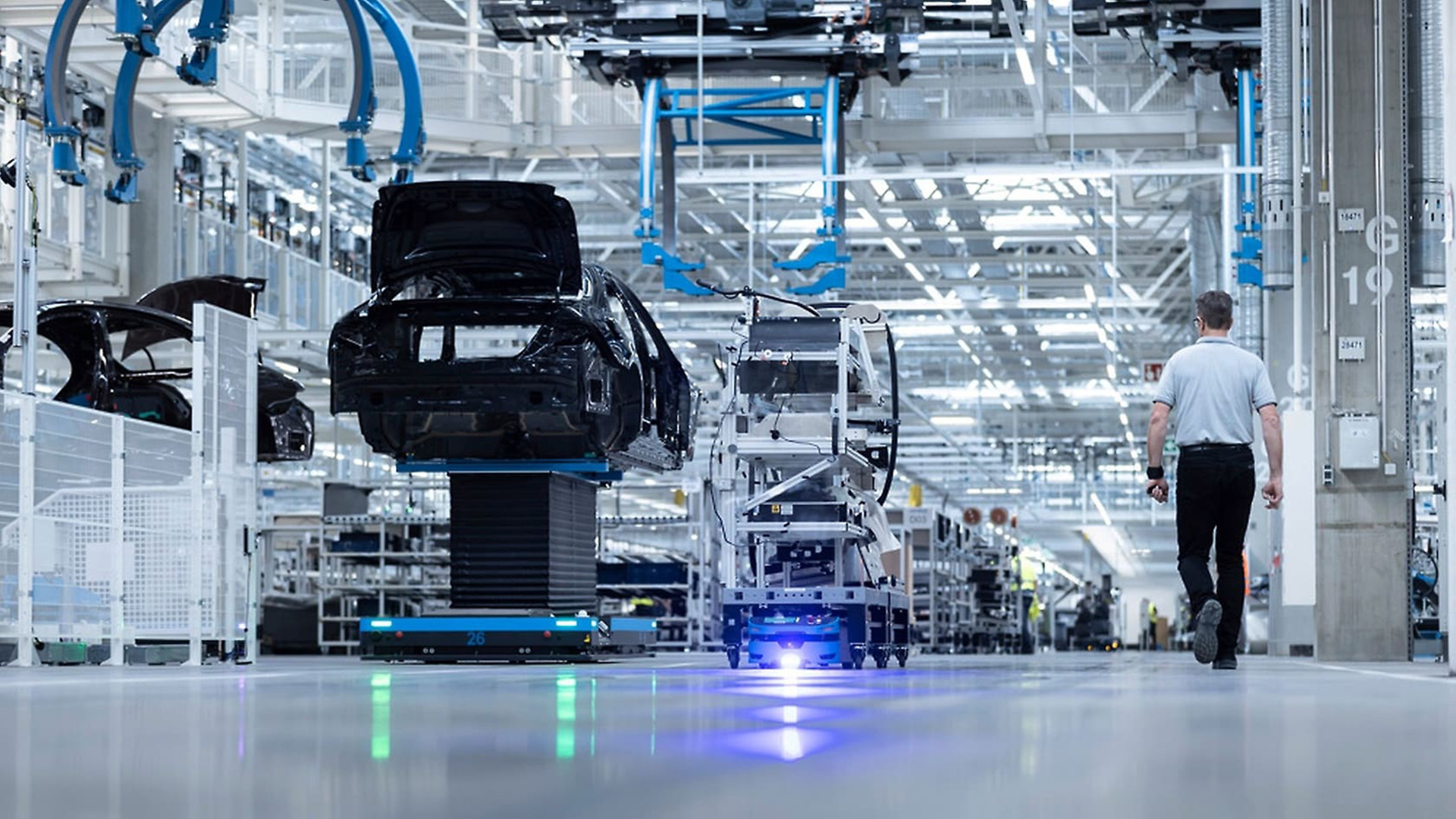
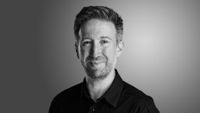
The Mercedes-Benz Sindelfingen site just outside of Stuttgart in Germany, has been building cars since 1919. Every Mercedes S-Class has been built here since its inception in 1972 and the classic 300SL Gullwing was also a product of this facility.
The Sindelfingen site is the size of a small town, covering over 3,000,000m2 and employing over 35,000 people. It has its own restaurants, a kindergarten, two fire stations and a petrol station. It also has two test tracks where new models can be put through their paces, away from prying eyes.
Among the hundreds of R&D and production buildings sits the giant Factory 56. This is where Mercedes-Benz’s premium models are produced and is the most advanced production facility that Mercedes owns. I was given the opportunity to be among the first journalists to see inside the factory.
Factory 56
Built in 2020, Factory 56 covers over 220,000m2 – or about the size of 30 football fields. It is designed to be the most efficient and sustainable factory of its kind, with 40% of its roof covered with 12,000 solar panels that account for 30% of the building's power requirements. The rest come from green sources elsewhere. Giant batteries can store up to 1,400kWh of power too.
The design includes recycled concrete and skylights to keep the factory floor bright, all part of the blue-sky architecture. 400 autonomous guided vehicles (AGVs) buzz around the floor on guided tracks, delivering parts to different stations, while the cars are lifted by giant cradles that tilt them on their side for work on the underside, and then progress down the giant travelator, while crews of mechanics fit different parts to the cars.
The production line currently includes four different models: the S-Class, the S-Class limousine, the S-Class Maybach and the all-electric Mercedes EQS. The production line is completely flexible though, and could add a new model within 48 hours. Interestingly all the SUV variants – including the EQS SUV and EQE SUV – are made in the North American factory rather than here in Germany.
Looking down the line, no two models were the same. There were left-hand drive models, right-hand drive models, US-spec cars (with a green button in the trunk for anti-kidnap protection), Chinese-specced cars, AMG models, petrol, diesel and electric drive trains. Black remains the most popular choice of colour though, with almost every model in versions of the paint finish, with the odd white model mostly in the AMG and EQS variants.
Get all the latest news, reviews, deals and buying guides on gorgeous tech, home and active products from the T3 experts
Tilting cradles allow work underneath the cars
The engines and drive trains are built at a separate factory in Stuttgart itself and transported to Sindelfingen by truck. The first stage of the process is Factory 56 is a marriage of the bodywork (created in another building) and the drivetrain. It’s a process that takes just 50 seconds through a mix of automated and manual screws.
As the cars go down the line, the various parts are attached by hand. Each car has a barcode and QR code on it so that the fitting crews can check the details, and the main spec, including the model type and destination country also shows on screens above each car.
Solar panels on the roof of Factory 56
At stage 356, I watched the famous three-pointed star badge being added to the bonnet of the S-Class and Maybach models. There are also filling stations on the production line that add not only fuel but also brake fluid, washer fluid and air conditioning liquids to the cars.
These cars are all made to order. Production only starts once the customer has signed their contract and their individual car can be easily tracked at every stage of the production process. Those finished models heading to Asia and North America (the biggest markets for these premium models) are transported by train to the ports.
The customer service centre, Mercedes-Benz Sindelfingen
For models staying here in Germany, customers are given the choice of collecting it from their local dealer or picking it up from the factory itself. Next to the large customer centre, a welcome lounge houses the cars ready to be picked up, and there’s even a photo area next to a giant three-pointed star, where new owners can take their first picture.
While the sustainability and design of Factory 56 are hugely impressive, it’s the adaptability of the product line that makes this interesting. It means that it is perfectly placed to adjust production levels as electric models grow in popularity – and also scale it back if interest wanes.
Ultimately in just a few years, the majority of the cars coming out of Factory 56 will be electric vehicles, as they will be through all of Sindelfingen and other Mercedes factories. While Mercedes’ premium models come in hybrid forms, its all-electric offerings – the EQ range – have a different look and feel to the standard cars. Factory 56 has shown that swapping between the models for production isn’t a problem and so whatever form the next car takes, it will be ready.
As T3's Editor-in-Chief, Mat Gallagher has his finger on the pulse for the latest advances in technology. He has written about technology since 2003 and after stints in Beijing, Hong Kong and Chicago is now based in the UK. He’s a true lover of gadgets, but especially anything that involves cameras, Apple, electric cars, musical instruments or travel.