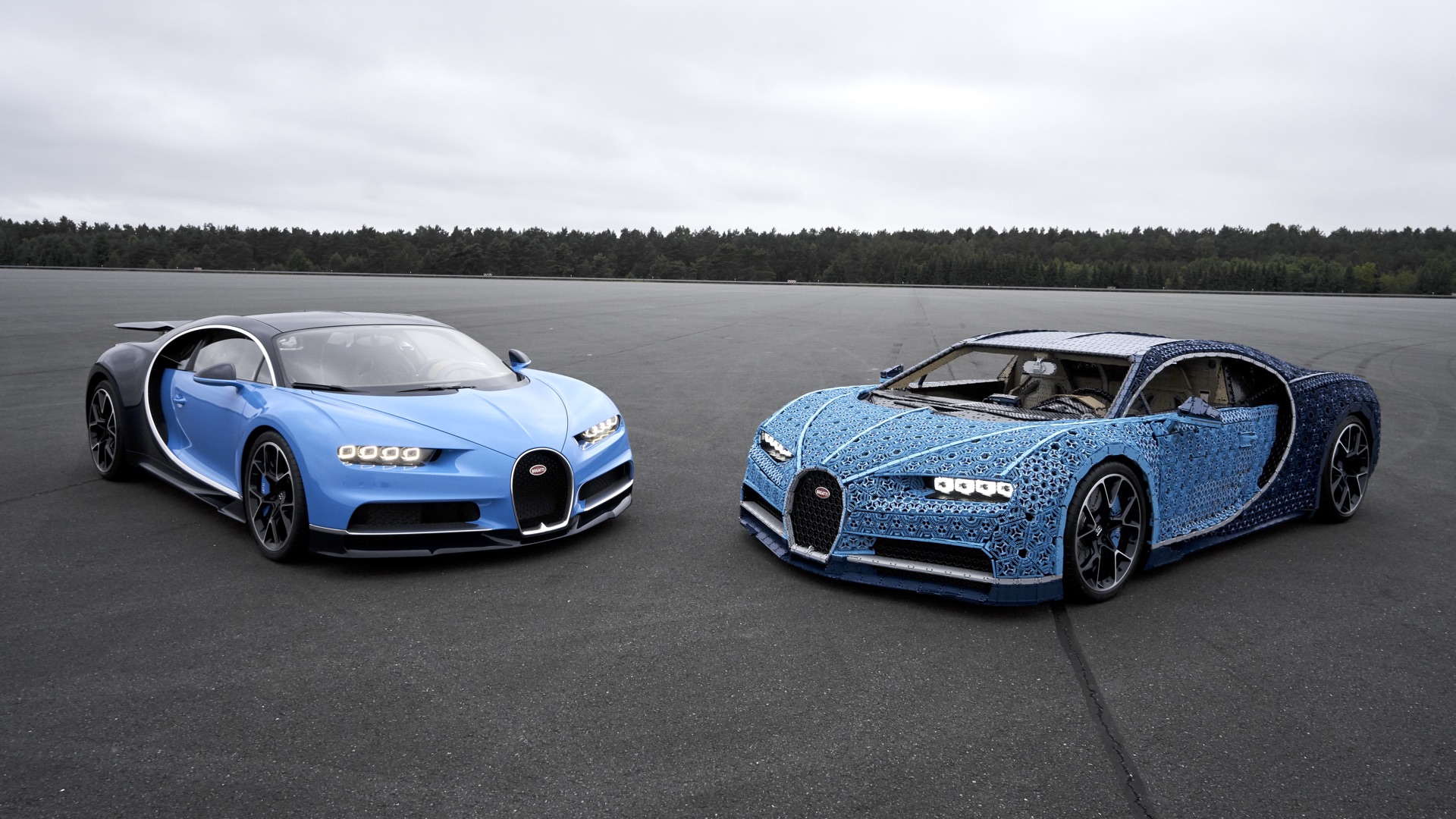
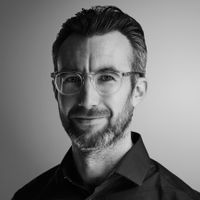
Not long after Lego announced that its next super-deluxe Lego Technic model would be a Bugatti, it invited us to the car maker's test track in deepest Germany. Not to see the small model, but something much more mind-blowing.
Lego has built, from over a million individual pieces of Technic, a life-size Lego Bugatti Chiron… that actually drives.
Weighing around 1,500kg, it's built pretty much solely from Technic pieces, with the exception of a steel frame (necessary for supporting all that weight), wheels (necessary for being round in a way that Lego is not), hydraulic brakes, power steering, a roll cage (just in case), and a few other mechanical pieces that can't really be made of plastic.
It's the first Lego creation of this kind of scale to be built without using glue to hold the pieces together, and that also means it's the first time Lego had to build load-bearing sections purely from Technic.
And even more impressive than all that? It was so complex that the computer modelling systems the team normally uses couldn't handle all of the design, so most of it was planned by hand. Parts were iterated as they were being put together, to get them perfect.
"The first beams were just built on a table, and we were testing the properties of them, and what they could withstand," explained Pavel Volný, an engineer on the project. "And then when we saw some potential in having a really strong one, we started to build some structures."
Testing load-bearing beams the low-tech way
We were curious how the team kept track of how it was going to look and fit together at the final stages with no fully planned model to refer to. "We almost lived together for like a quarter of a year," said Pavel. "We were discussing things ad hoc, on the spot. We had to be sure that each and every member of the team had the right information, at the right time.
Get all the latest news, reviews, deals and buying guides on gorgeous tech, home and active products from the T3 experts
"It was really challenging to keep everything on track, to keep in mind what we had done or adjusted. But it was possible," he added.
Starting a structure
The need for the car to support its own weight on Lego connections alone led to some complications in the way it was built, from the centre out. For a start, the body isn't connected to the steel frame in any fixed way: it just sits on it, held in place by gravity. But, given that the idea was always that should drive, it also needs to not slide off in motion.
This means that the underpinnings of the rear section and the cockpit are actually built to wrap around the frame in places, locking the body into place. But these areas take a lot of stress. "When we build models with [the regular] Lego system, it’s glued. This time, it was Lego Technic, and not glued. And so we had to come up with the type of bricks that were the strongest from a structural point of view," Pavel told us. The team tried different versions of Technic structural builds, that could withstand more force than the plastic was ever designed for.
The different, mostly modular, pieces start to come together
This approach meant that once they started building on top of that core structure, they were kind of stuck with it. "In the beginning, we had to make a lot of decisions with the design crew, and with manufacturers, because we knew that it wouldn’t be easy – or even possible – to change things," explained Pavel. "As the guy who is responsible for the stiffness and for safety of the construction, some things are very necessary [for my work]. So it was by quid pro quo that [the designers] gave me something, and I gave them something else.
"If you want to change some special part which is inside, I’m not sure if you’d be able to reach it, honestly. But we went with this risk, and we decided that we definitely need to change the engine and make it easy to change it."
So many motors
The engine is a feat of engineering in itself. The car is equipped with an absolutely monstrous power pack of Lego Technic Power Functions motors. Normally, these make conveyer belts move on models a couple of feet long. Here, they make a full-size car drive.
The trick is sheer numbers: over 2,300 Technic motors are connected into one huge engine block. This is divided into 24 motor packs, each comprising 96 individual motors. This configuration enables them to run off a higher-power battery than they're normally designed for, spreading the voltage out across the parallel configuration.
Each motor pack contains 4,032 individual Lego gears to apply the power (that's 96,768 in total). Everything is held together with Lego too, with just a few essential non-Lego parts: Teflon washers, a 3D-printed carbon fibre gear wheel, and a steel chain to provide the force from the motors to the drive shaft.
The end result is a whopping 5.3 horsepower, developing an estimated 96Nm of torque, aimed to push the car up to around 30kph. This, admittedly, does not quite match the 1,479 horsepower and 400kph (248mph – and that's electronically limited) of the real Bugatti.
Unsurprisingly, managing even this much from toy motors was one of the biggest challenges of the whole thing. To get an idea of where to start, they looked at the expected physics. "We were calculating velocity, the resistance of the wheels on the tarmac and some other things," Pavel said.
Even the detail on the brakes has been recreated in Lego
"So we came up with some numbers, and then we compared them to the actual physical properties of one Power Functions large motor, multiplied it by a coefficient of safety [basically, an engineer's margin for error] to make it work. And then we got some number. It's a simple version. Let's put it that way."
In fact, the engine was the most challenging part of all from a mechanical perspective, and not just because it includes well over 10,000 parts connected intricately. The first version was running way too hot: 70°C. The motors couldn't be changed for something else, and it couldn't be made much larger, so the team experimented with reducing friction. They ended up using the Teflon washers and silicon grease around the rotating parts, and this helped get the temperature down to a safer 32°C.
Having conquered the trials of the structure and engine, one huge challenge still remained: how to mimic the sleek, curved look of the Chiron using the distinctly square angles of Lego.
The colour was easy (relatively) – Technic pieces had to be specially created in the correct hues to copy the look of the real Chiron. But they were still the same hard shape.
The result is the most visually spectacular aspect of the entire car, and is the thing that still blows me away in its ingenuity every time I think about it: they created a Lego fabric.
You can see the intricacy that went into creating a layer of Lego that moves like a cloth
The mottled effect you see in these pictures is because the Lego Chiron has an outer 'skin' that's made of Lego Technic triangles, in two different sizes, tessellated together. Held out flat, they flex, like a woven material.
The car itself, then, has an underframe of Lego, with a series of pillars sticking out from it, at different heights. The 'skin' is mounted onto these pillars, and so the way it sits over them creates the necessary curve.
Under the skin: the car without its outer layer
Each of the pillars is actually a linear actuator, which means they can all have their heights individually adjusted, by reaching through the gaps in the skin and screwing. It means the skin's shape can actually be fine-tuned even when it's on the car, to make sure the organic look is perfect. (Originally, this was done. by hand, which was wrecking the team's wrists, but a drill was too powerful to do it precisely… so they built a custom low-power drill just for this purpose out of – you guessed it – Lego.)
Recreating the look is even more meticulous in other areas. To echo the carbon fibre weave areas on the original car, a special weave of Lego was created for those parts. To create the dramatic rear lights, the first ever transparent Lego Technic bricks had to be produced.
The faux carbon effect and transparent rear lights
That wasn't the only extra mile the Lego team went to for the lights. They run on an electrical system that makes them light up in a pattern that copies exactly they the original Chiron lights up when turned on.
The front lights, still in the testing phase
The final, crucial detail to get right was the rear wing. The Lego car's 5hp may mean it doesn't have need for a dramatic air brake, but it's not a Chiron without one. The Lego car's is pneumatically powered, with the air stored in eight Lego Technic pneumatic tanks. They take a few seconds of priming (controlled through an app, which talks to an electrical control unit that's basically an adapted smart home controller), but then you can raise the wing to its brake position.
It's really more for show, admittedly…
Agonisingly, our visit to the test track was on the only rainy day all summer there, meaning we couldn't test the drivability (and comfort of that all-Lego interior, painstakingly mimicking the original). That's the peril of a gappy plastic electric car.
Here's a gallery with more pics of the car, in development and the final version, out on the tarmac.
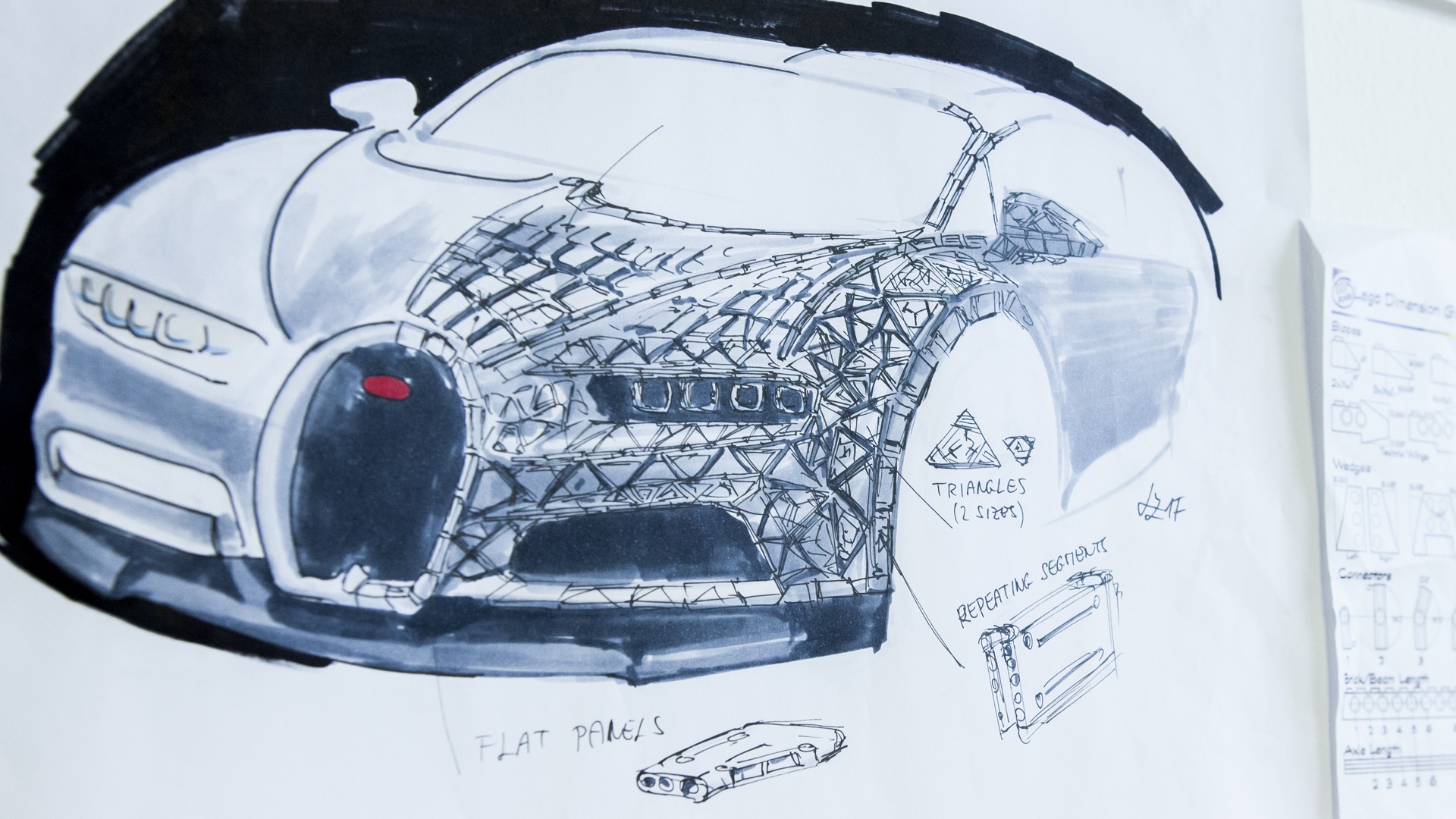
Early concept drawings for the 'skin'
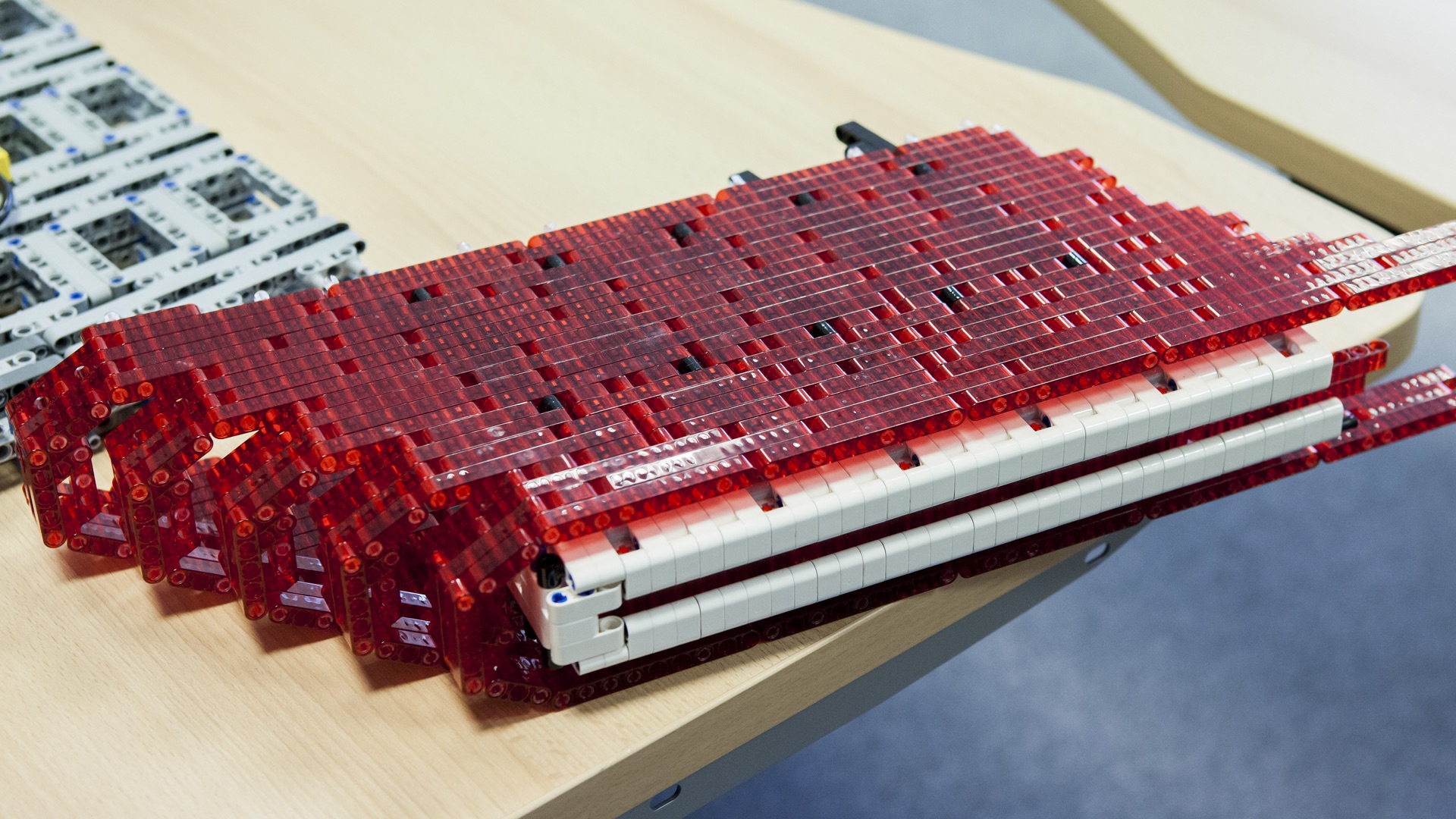
The rear light strip in progress
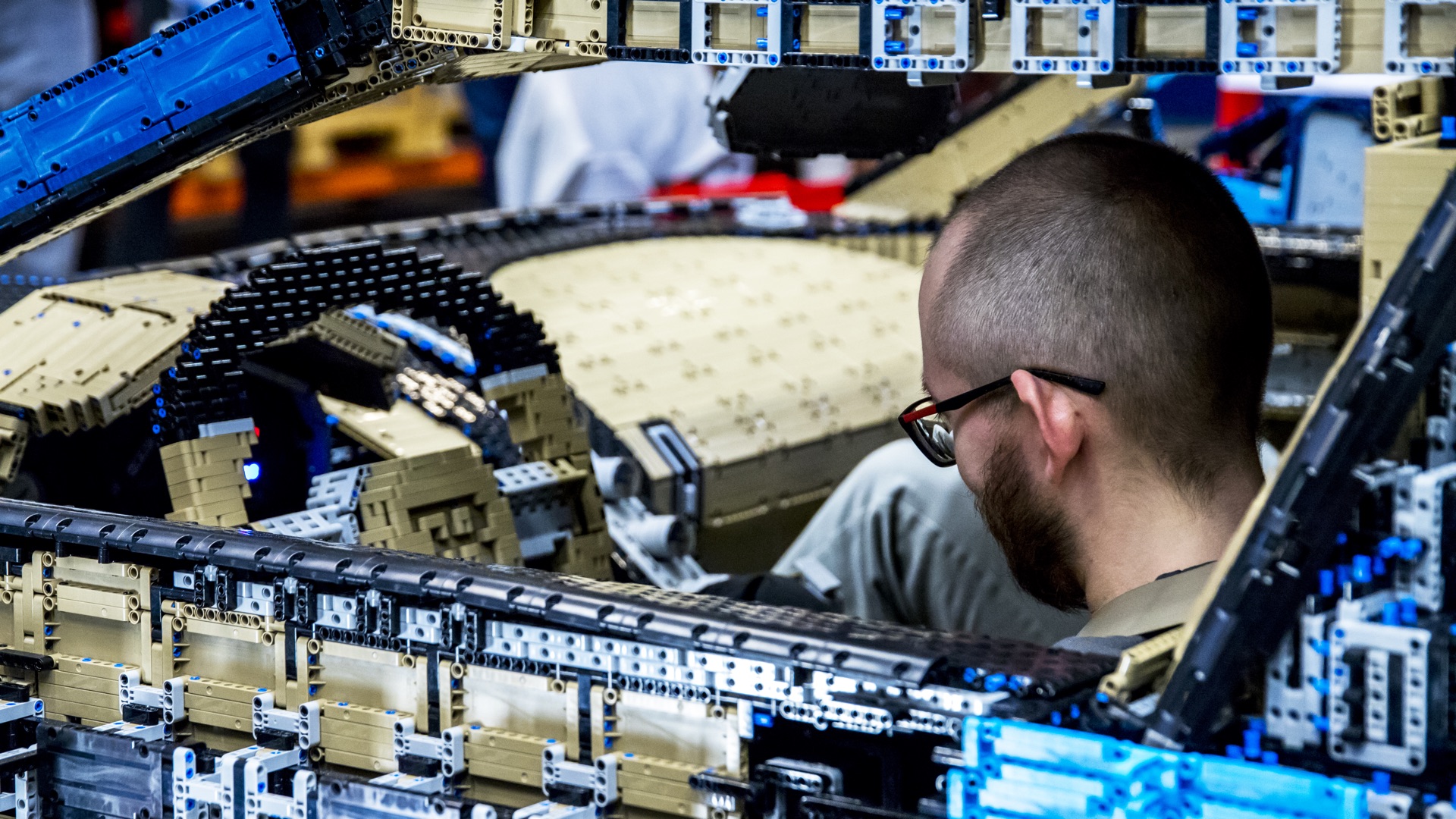
Testing the interior
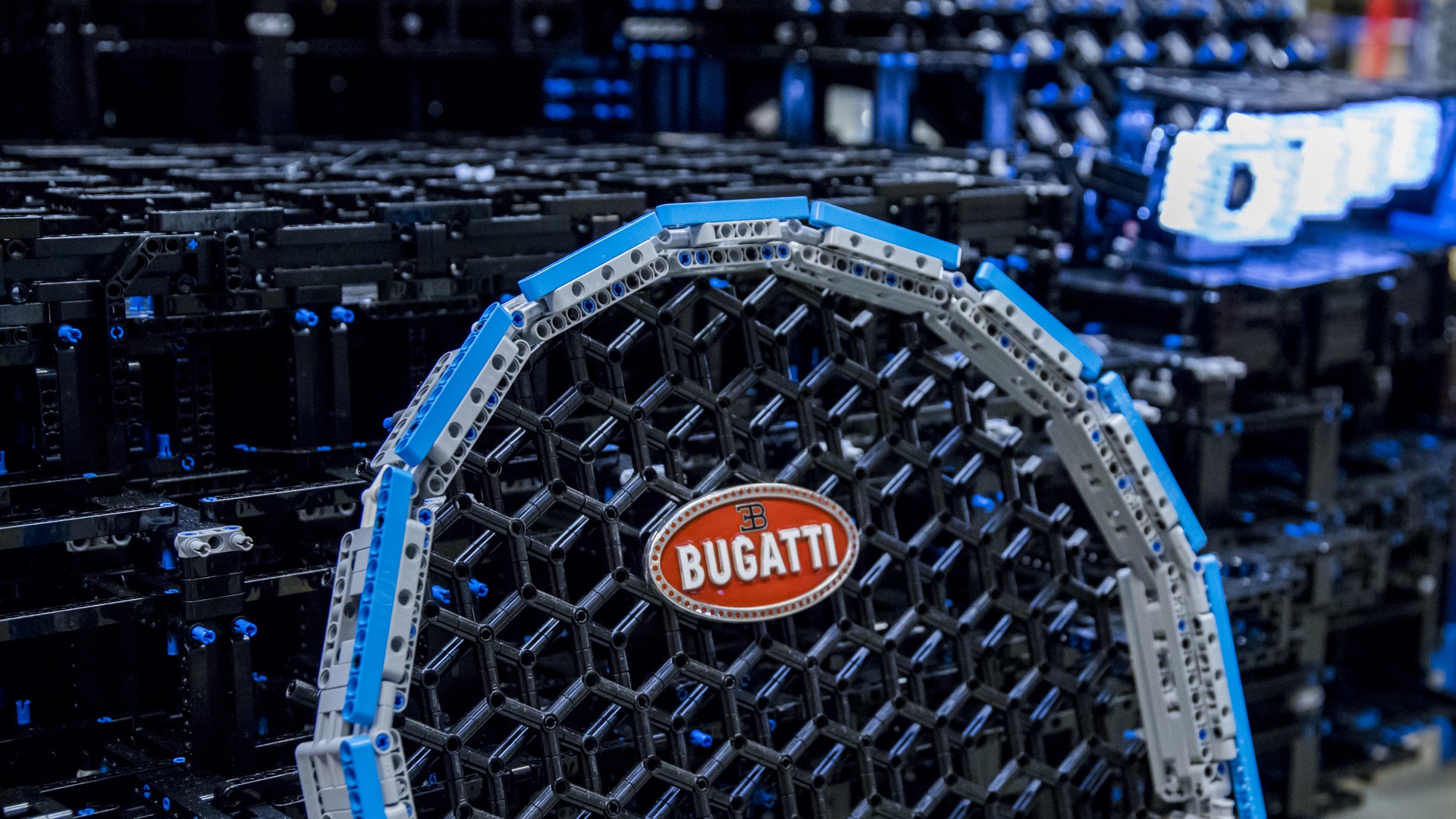
The iconic grille
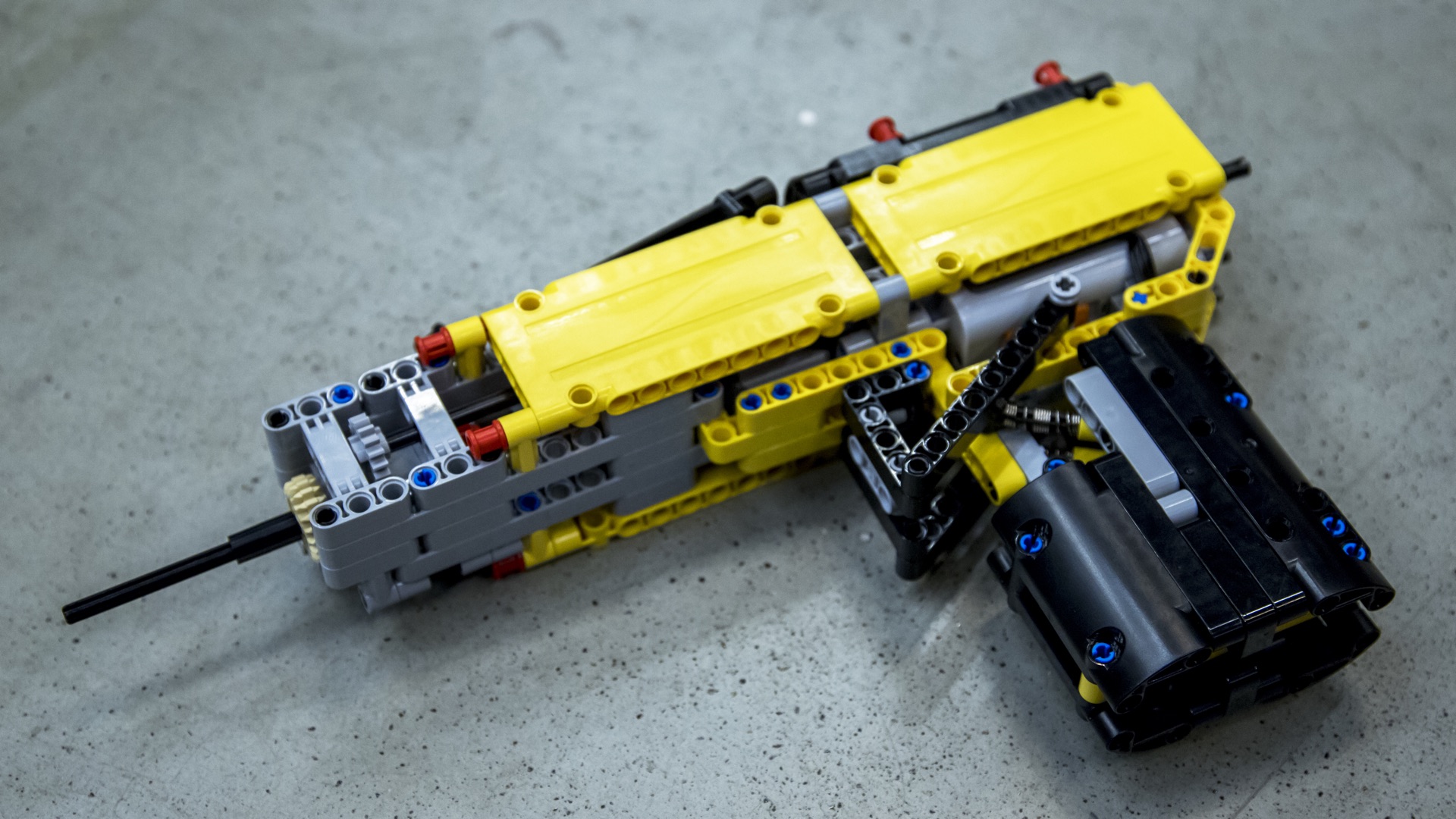
The self-built tool for tweaking the bodywork
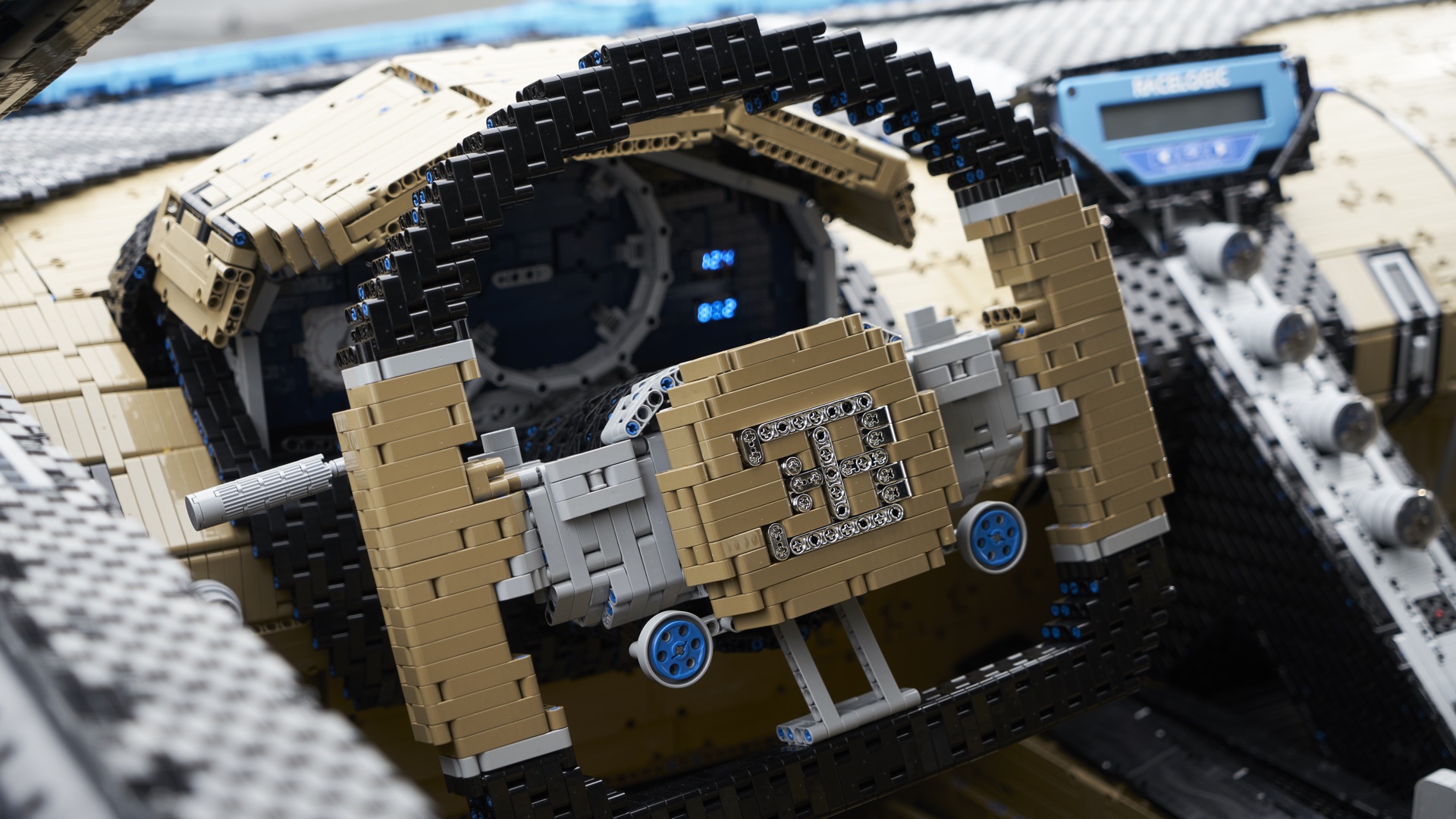
The steering wheel and instruments
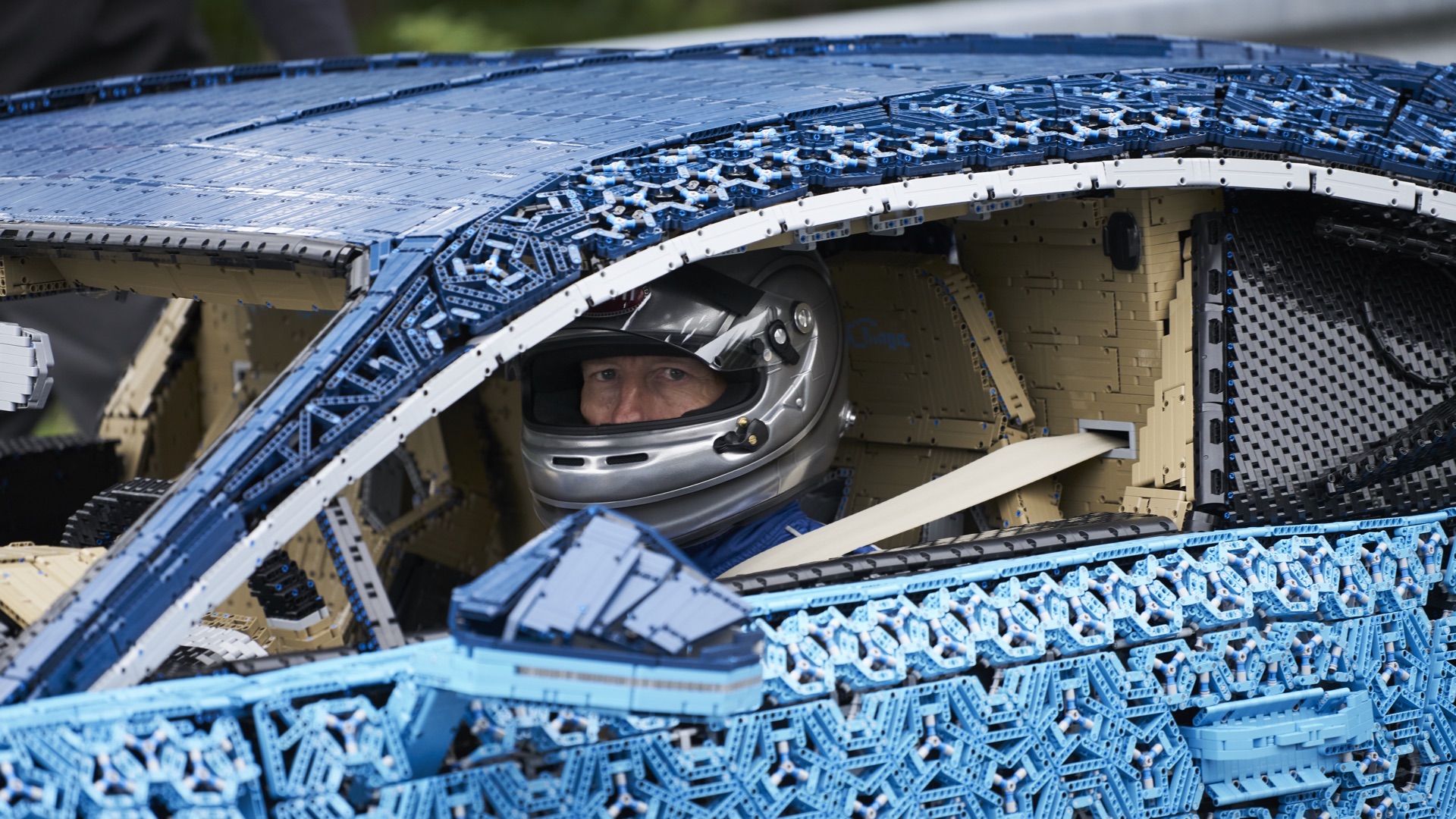
Ready to roll on the track
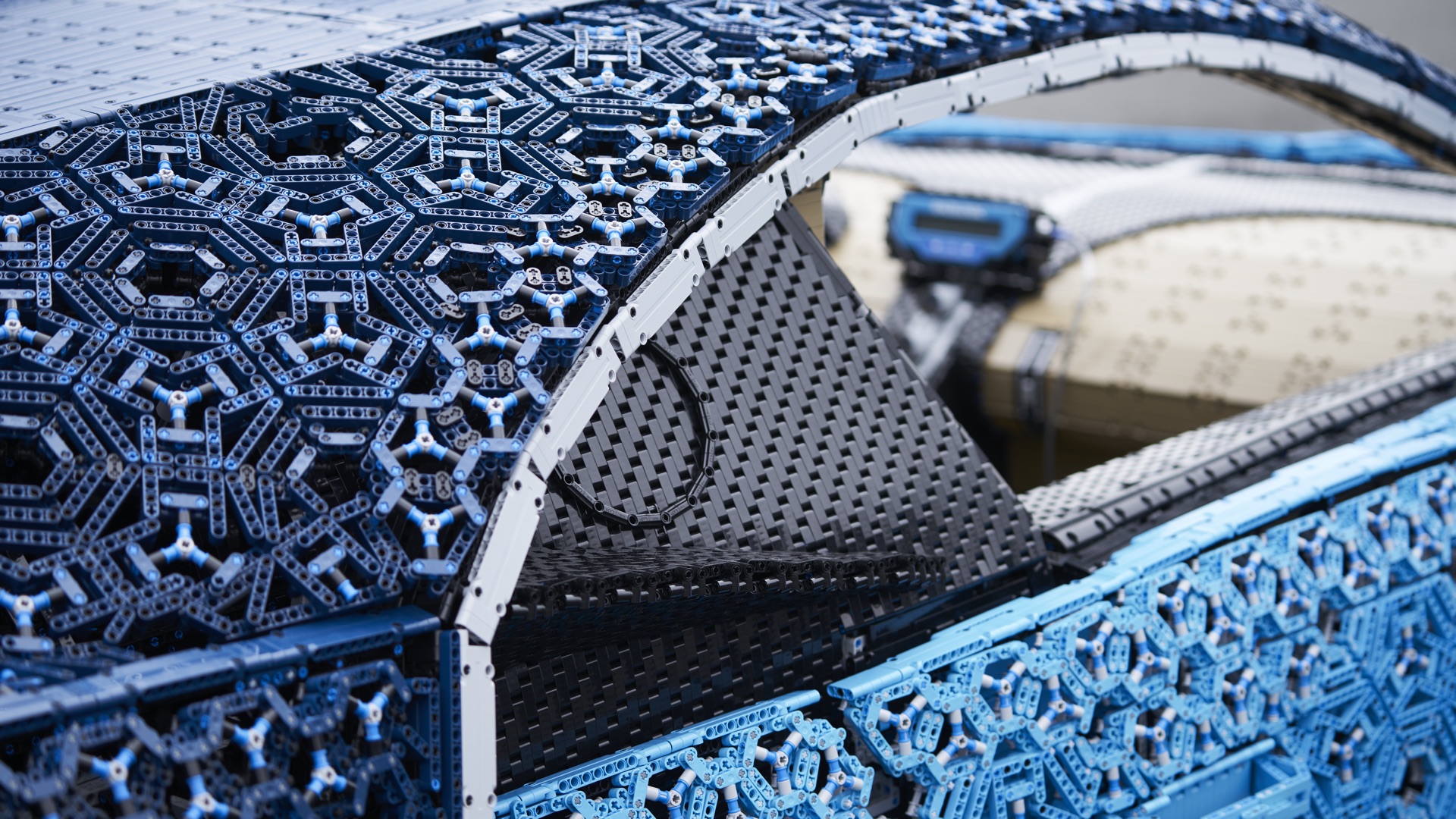
The skin and faux carbon fibre
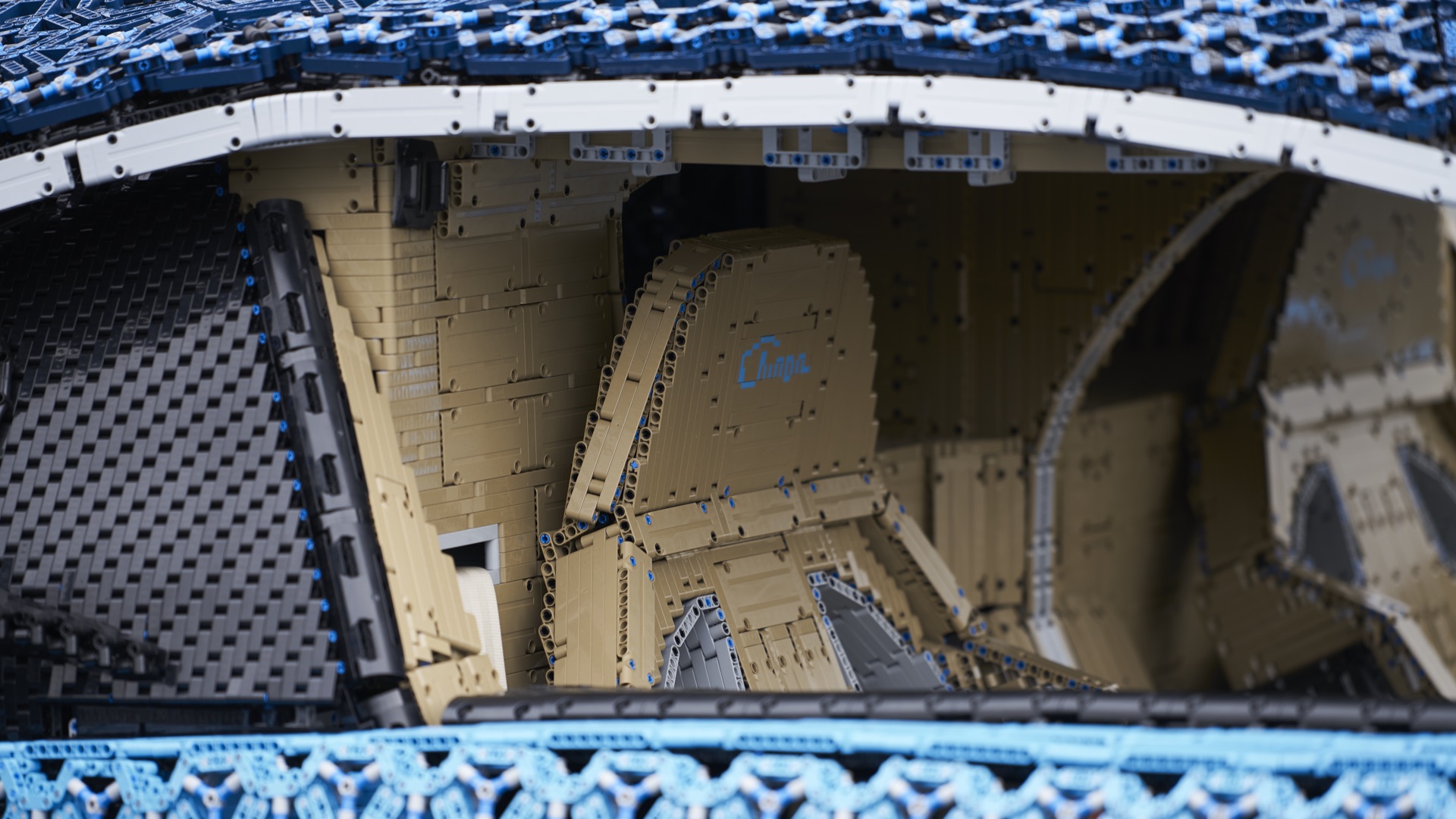
Fully detailed Lego leather seats
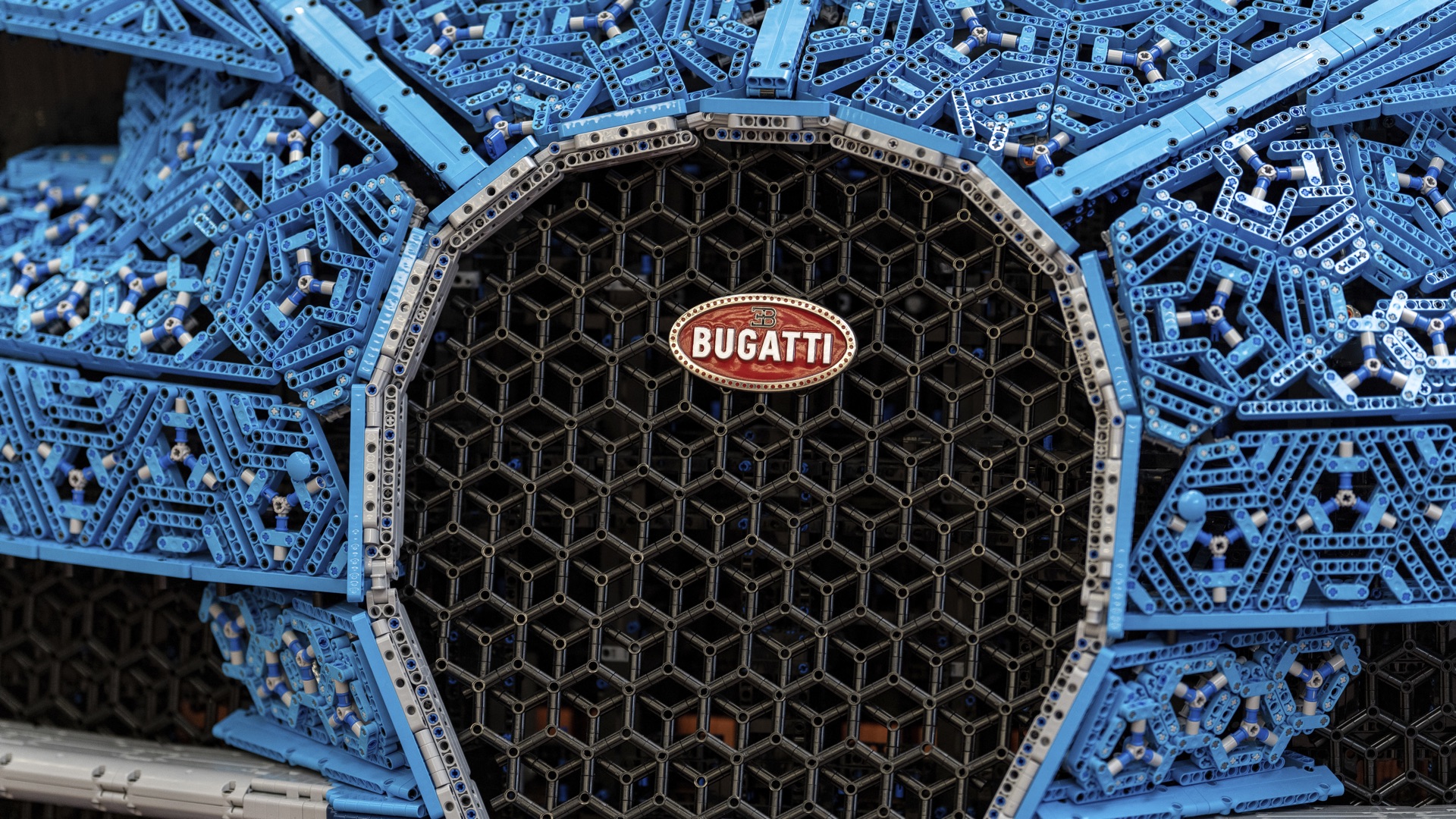
The grille, complete
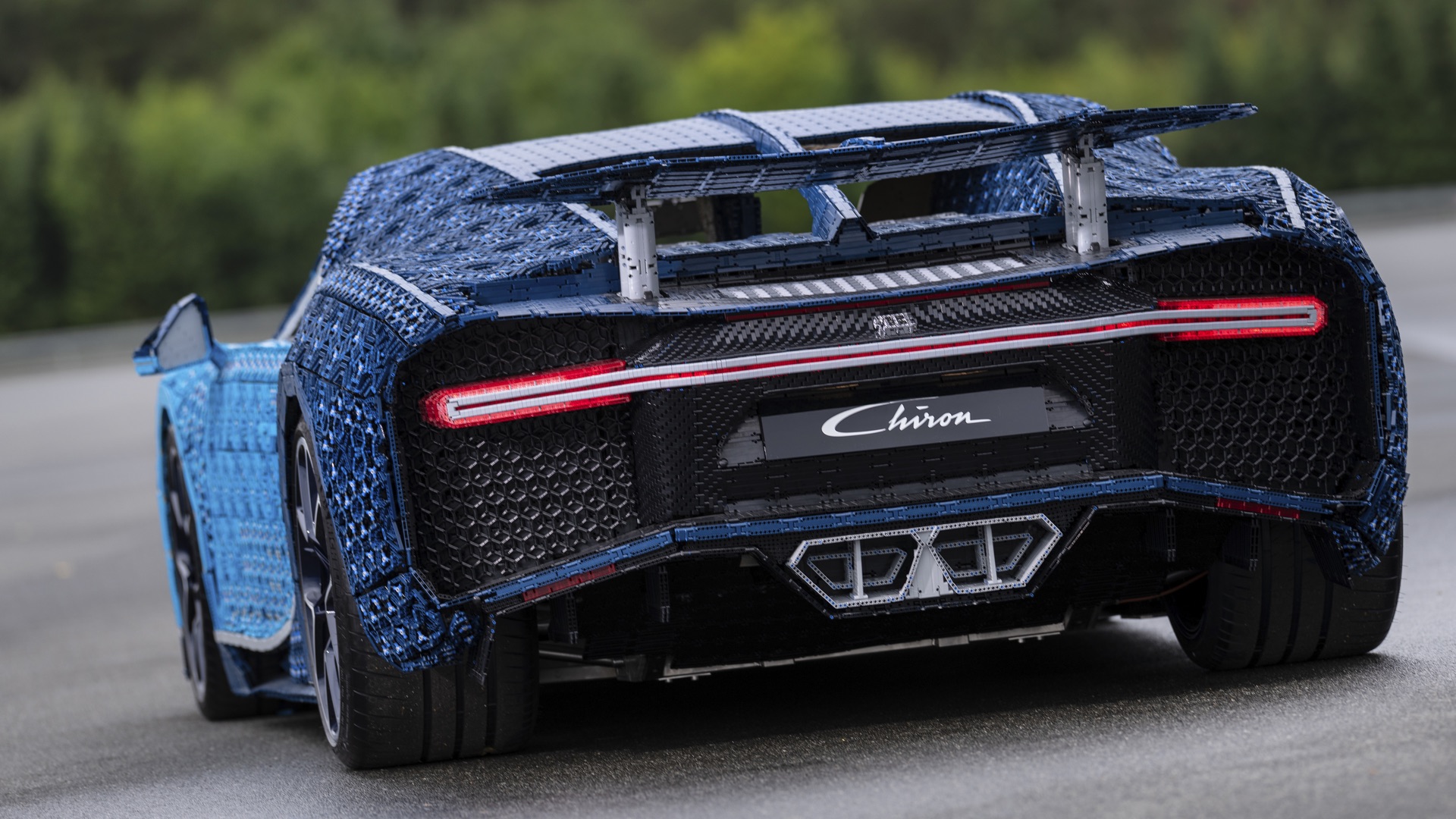
Finished and on the track
Matt is T3's former AV and Smart Home Editor (UK), master of all things audiovisual, overseeing our TV, speakers and headphones coverage. He also covered smart home products and large appliances, as well as our toys and games articles. He's can explain both what Dolby Vision IQ is and why the Lego you're building doesn't fit together the way the instructions say, so is truly invaluable. Matt has worked for tech publications for over 10 years, in print and online, including running T3's print magazine and launching its most recent redesign. He's also contributed to a huge number of tech and gaming titles over the years. Say hello if you see him roaming the halls at CES, IFA or Toy Fair. Matt now works for our sister title TechRadar.